Here are some pros and cons of pallet racking types:
Pro
Cons
Double Deep
- Easy to Assemble
- High pallet storage density
- Relatively low cost storage solution
- Max height 11m
- Visibility of pallets stored at height is difficult – may cause problems such as product damage, reduction of productivity
- Accessibility is less – products can be hidden and become lost without good inventory and location tracking
- Not useful for picking, pallets need to be moved to get to pallets at the back
Push back
- A variety of forklift trucks can be used
- Increases pallet density by reducing aisles
- Less expensive than live storage
- Produce damage possible
- Accessibility is lower – good inventory needed to avoid losing stock
- Danger of rear-drive forklift trucks climbing under itself during put away
- Carts need to maintenance
- Vertical height is lost due to the slope of the rails
Live Storage
- Good for FIFO (First In First Out)
- Storage density high, less aisle space needed
- Great for reducing replenishment for picking (stock is replenished from one side and picked from the other)
- Pallets can be broken, it is essential to have good quality pallets to avoid this
- Wheels and brakes need regular maintenance
- Vertical height is reduced due to slope
Narrow Aisle Racking
- Frees up to 45% of the floor space
- Although you need a specialist narrow aisle forklift truck, they lift higher and work faster than a regular lift truck
- Accessibility of all pallets
- Good stock rotation
- Max height of 11-15m
- You need a narrow aisle forklift truck to use with the system
- Forklift truck needs a guiding system with rails or wires
Drive In
- Ultra high density storage, utilisation can be up to 80% of warehouse volume
- Can be designed to suit any pallet size
- Max height 10m
- Works with the First In Last Out (FILO) principle, this is ideal for companies with pallets of similar SKUs
- Restricted to 7-10 pallets deep
- Height can be restricted to allow practical usage
- Guide rails maybe needed to protect from damage
- Accessibility to pallets can be restricted
- May require multiple handling of stock to maximise utilisation
Adjustable Pallet Racking
- Cheapest system
- Can store up to 11m high
- Quick to install
- No specialised truck needed
- Good picking with 100% access to all storage locations
- Poor net area utilisation – only 30% of available area
Satellite storage
- High density storage, up to 40 pallets deep can be possible
- Advantage over Drive In as it de-couples the forklift from the storage system. The truck never has to enter the rack or touch the rack. Saving huge amount of labour time
- Accident are also eliminated
- Maximum height 11m
- Storage and retrieval done by satellite, eliminating possible impacts
- Efficient, time saved by non entering, forklift trucks can be left to other tasks
- Cost effective
- Can be First In First Out (FIFO) or First In Last Out (FILO)
- Higher initial investment
- No direct access to pallets
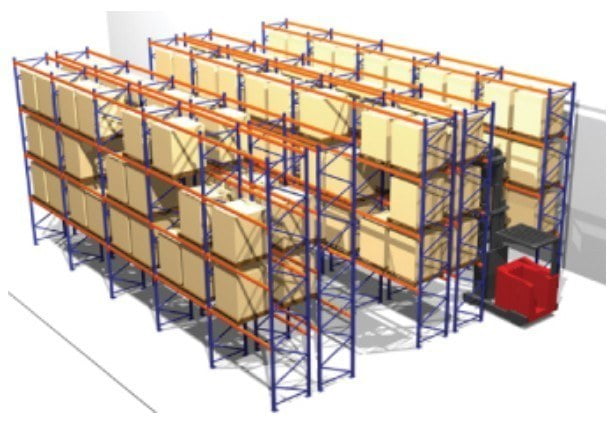
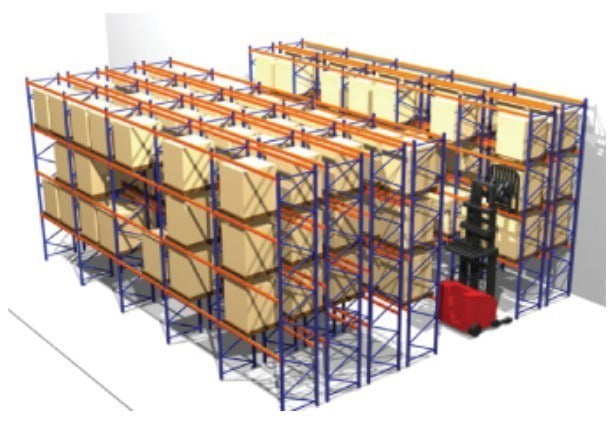
The Double Deep system requires the use of a specialist truck with an attachment fitted. Also, the aisles having to be bigger than normal.
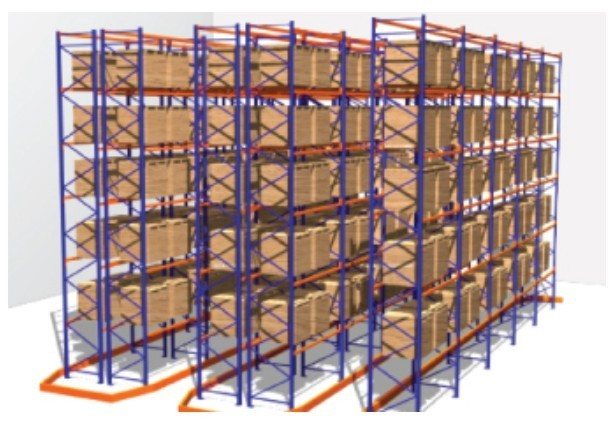
If you are using a specialist VNA machine this requires a super flat floor and for the machine to operate within the aisle you need to fit guide rails, standard or low profile, or use wire induction guidance system. You would need a secondary truck like a counter balance to load the vehicles which means fitting P&D stations to the racking is recommended.
There are two other trucks on the market called a “Flexi” or “Bendi” truck which are designed like a counter balance truck but bends in the middle making it able to operate in narrow aisles. These do not need guide rail or guidance aid and can operated outside which means one truck can do all.

The down fall to this system means you have limited stock rotation and order picking selectivity. You have to unload and load the system in a sequence making picking slower than other pallet racking systems. Conventional forklift trucks which can drive into the racks are used for picking and replenishment. Although immediate access to every product is not possible, drive-in racking plays a major role. Drive in racking can also be used as drive-through racking which means both sides of the racking can be used, if the racking unit is freestanding.
Drive-through racking offers the advantage that picking and replenishment can take place independent of each other which means you can create more pick faces.
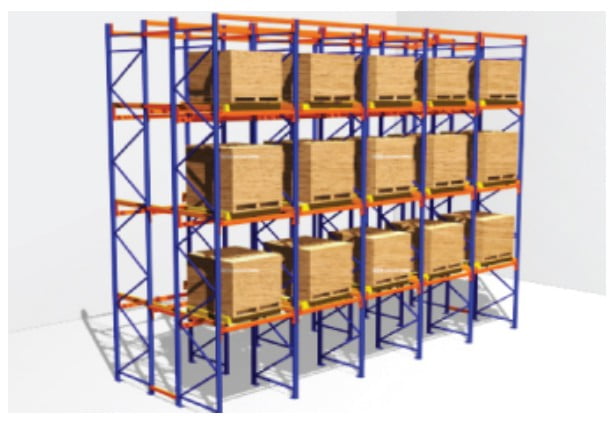
Push-back is ideal for storing medium-turnover products, using the Last In First Out (or LIFO) system. This is a moving system, so beware that things can go wrong. Debris can get onto the roller track causing the trolleys to jam.
If pallets are put away incorrectly then you can cause the trolley to twist and jam. This system needs to be maintained. Also, because this system is specialized and some forklift operators have not used it before we recommend that training be given.
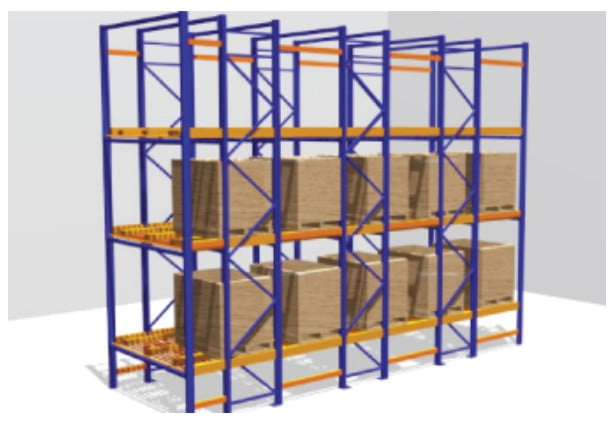
Live Storage system provides excellent volume utilization on First-In First-Out (FIFO) principle. It’s ideal for creating loads ready to out. As soon as the first pallet is removed then it releases the pallets behind to roll down ready for takeoff. This makes picking efficient and quick.
This system is not ideal for storing goods for over a length of time as the weight of the pallets embeds the wooden pallet on the rollers creating grooves in the wood, which means when the first pallet is taken off the pallets behind can get stuck. This is a moving system, so beware that things can go wrong. Debris can get onto the roller track causing the rollers to jam. If pallets are put away and slammed down onto the rollers then this will damage them causing them to break.
Some systems have a paddle mechanism at the front which separates the pallets behind from the first pallet at the front. If the first pallet is not taken off correctly then it will not release the pallets behind. The first instinct for the forklift operator to do is place the pallet back to its take off position to try again. Whilst doing this the operator can catch the paddle and bend it back breaking the mechanism. Once again this system needs to be maintained. Also, because this system is specialised and some forklift operators have not used it before we recommend that training be given.